1. Under what situation shall engineers use jacking at one end only and from both ends in prestressing work?
During prestressing operation at one end, frictional losses will occur and the prestressing force decreases along the length of tendon until reaching the other end. These frictional losses include the friction induced due to a change of curvature of tendon duct and also the wobble effect due to deviation of duct alignment from the centerline. Therefore, the prestress force in the mid-span or at the other end will be greatly reduced in case the frictional loss is high. Consequently, prestressing, from both ends for a single span i.e. prestressing one-half of total tendons at one end and the remaining half at the other end is carried out to enable a even distribution and to provide symmetry of prestress force along the structure. In fact, stressing at one end only has the potential advantage of lower cost when compared with stressing from both ends. For multiple spans (e.g. two spans) with unequal span length, jacking is usually carried out at the end of the longer span so as to provide a higher prestress force at the location of maximum positive moment. On the contrary, jacking from the end of the shorter span would be conducted if the negative moment at the intermediate support controls the prestress force. However, if the total span length is sufficiently long, jacking from both ends should be considered.
 |
Under what situation shall engineers use jacking at one end only and from both ends in prestressing work |
2. What is “preset” during installation of bridge bearings?
“Preset” is a method to reduce the size of upper plates of sliding bearings in order to save the material cost. The normal length of a upper bearing plate should be composed of the following components: length of bearing + 2 x irreversible movement + 2 x reversible movement. Initially the bearing is placed at the mid-point of the upper bearing plate without considering the directional effect of irreversible movement. However, as irreversible movement normally takes place at one direction only, the bearing is displaced/presetted a distance of (irreversible movement/2) from the mid-point of bearing in which the length of upper plate length is equal to the length of bearing + irreversible movement + 2 x reversible movement. In this arrangement, the size of upper plate is minimized in which irreversible movement takes place in one direction only and there is no need to include the component of two irreversible movements in the upper plate.
Note: “Preset” refers to the displacement of a certain distance of sliding bearings with respect to upper bearing plates during installation of bearings.
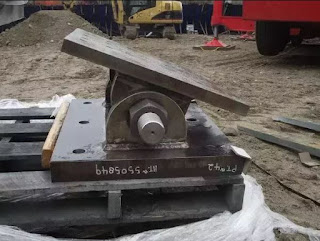 |
What is “preset” during installation of bridge bearings |
3. In incremental launching method of bridge construction, what are the measures adopted to enhance sufficient resistance of the superstructure during the launching process?
(i) During the launching process the leading edge of the superstructure is subject to a large hogging moment. In this connection, steel launching nose typically about 0.6-0.65 times span length is provided at the leading edge to reduce the cantilever moment. Sometimes, instead of using launching nose a tower and stay system are designed which serves the same purpose.
(ii) The superstructure continually experiences alternative sagging and hogging moments during incremental launching. Normally, a central prestress is provided in which the compressive stress at all points of bridge cross section is equal. In this way, it caters for the possible occurrence of tensile stresses in upper and lower part of the cross section when subject to hogging and sagging moment respectively. Later when the whole superstructure is completely launched, continuity prestressing is performed in which the location and design of continuity tendons are based on the bending moments in final completed bridge condition and its provision is supplementary to the central prestress.
(iii)For very long span bridge, temporary piers are provided to limit the cantilever moment.
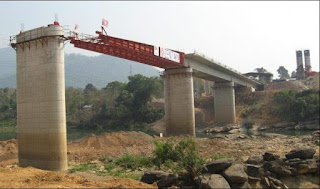 |
In incremental launching method of bridge construction, what are the measures adopted to enhance sufficient resistance of the superstructure during the launching process |
4. In bridge widening projects, the method of stitching is normally employed for connecting existing deck to the new deck. What are the problems associated with this method in terms of shrinkage of concrete?
In the method of stitching, it is a normal practice to construct the widening part of the bridge at first and let it stay undisturbed for several months. After that, concreting will then be carried out for the stitch between the existing deck and the new deck. In this way, the dead load of the widened part of bridge is supported by itself and loads arising from the newly constructed deck will not be transferred to the existing deck which is not designed to take up these extra loads. One of the main concerns is the effect of stress induced by shrinkage of newly widened part of the bridge on the existing bridge. To address this problem, the widened part of the bridge is constructed a period of time (say 6-9 months) prior to stitching to the existing bridge so that shrinkage of the new bridge will take place within this period and the effect of shrinkage stress exerted on the new bridge is minimized. Traffic vibration on the existing bridge causes adverse effect to the freshly placed stitches. To solve this problem, rapid hardening cement is used for the stitching concrete so as to shorten the time of setting of concrete. Moreover, the stitching work is designed to be carried out at nights of least traffic (Saturday night) and the existing bridge may even be closed for several hours (e.g. 6 hours) to let the stitching works to left undisturbed. Sometimes, longitudinal joints are used in connecting new bridge segments to existing bridges. The main problem associated with this design is the safety concern of vehicles. The change of frictional coefficients of bridge deck and longitudinal joints when vehicles change traffic lanes is very dangerous to the vehicles. Moreover, maintenance of longitudinal joints in bridges is quite difficult.
Note: Stitching refers to formation of a segment of bridge deck between an existing bridge and a new bridge.
5. What are the advantages of assigning the central pier and the abutment as fixed piers?
(i) For abutment pier to be assigned as fixed pier while the bridge is quite long, the longitudinal loads due to earthquake are quite large. As the earthquake loads are resisted by fixed piers, the size of fixed piers will be large and massive. In this connection, for better aesthetic appearance, the selection of abutment as fixed piers could accommodate the large size and massiveness of piers. Normally abutments are relatively short in height and for the same horizontal force, the bending moment
(ii) For the central pier to be selected as the fixed pier, the bridge deck is allowed to move starting from the central pier to the end of the bridge. However, if the fixed pier is located at the abutment, the amount of movement to be incorporated in each bearing due to temperature variation, shrinkage, etc. is more than that when the fixed pier is located at central pier. Therefore, the size of movement joints can be reduced significantly.
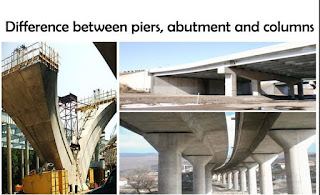 |
What are the advantages of assigning the central pier and the abutment as fixed piers |
6. Sometimes the side of concrete bridges is observed to turn black in colour. What is the reason for this phenomenon?
In some cases, it may be due to the accumulation of dust and dirt. However, for the majority of such phenomenon, it is due to fungus or algae growth on concrete bridges. After rainfall, the bridge surface absorbs water and retains it for a certain period of time. Hence, this provides a good habitat for fungus or algae to grow. Moreover, atmospheric pollution and proximity of plants provide nutrients for their growth. Improvement in drainage details and application of painting and coating to bridges help to solve this problem. Reference is made to Sandberg Consulting Engineers Report 18380/X/01.
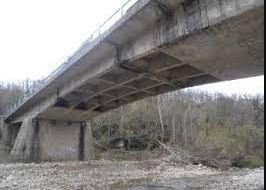 |
sometimes the side of concrete bridges is observed to turn black in colour. what is the reason for this phenomenon |
7. In prestressing work, if more than one wire or strand is included in the same duct, why should all wires/strands be stressed at the same time?
If wires/strands are stressed individually inside the same duct, then those stressed strand/wires will bear against those unstressed ones and trap them. Therefore, the friction of the trapped wires is high and is undesirable.
8. In the design of elastomeric bearings, why are steel plates inserted inside the bearings?
For elastomeric bearing to function as a soft spring, the bearing should be allowed for bulging laterally and the compression stiffness can be increased by limiting the amount of lateral bulging. To increase the compression stiffness of elastomeric bearings, metal plates are inserted. After the addition of steel plates, the freedom to bulge is restricted and the deflection is reduced when compared with bearings without any steel plates under the same load. Tensile stresses are induced in these steel plates during their action in limiting the bulging of the elastomer. This in turn would limit the thickness of the steel plates. However, the presence of metal plates does not affect the shear stiffness of the elastomeric bearings.
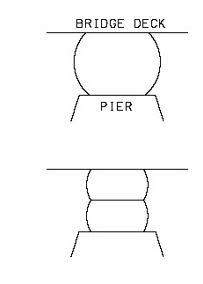 |
Effect of steel plate in elastomeric bearing. |
9. How to determine the size of elastomeric bearings?
For elastomeric bearing, the vertical load is resisted by its compression while shear resistance of the bearing controls the horizontal movements. The design of elastomeric bearings are based on striking a balance between the provision of sufficient stiffness to resist high compressive force and the flexibility to allow for translation and rotation movement.The cross sectional area is normally determined by the allowable pressure on the bearing support. Sometimes, the plan area of bearings is controlled by the maximum allowable compressive stress arising from the consideration of delamination of elastomer from steel plates. In addition, the size of elastomeric bearings is also influenced by considering the separation between the structure and the edge of bearing which may occur in rotation because tensile stresses deriving from separation may cause delamination. The thickness of bearings is designed based on the limitation of its horizontal stiffness and is controlled by movement requirements. The shear strain should be less than a certain limit to avoid the occurrence of rolling over and fatigue damage. The vertical stiffness of bearings is obtained by inserting sufficient number of steel plates.
10. In a curved prestressed bridge, how should the guided bearings in piers of the curved region be oriented with respect to the fixed bearing in abutment?
To determine the orientation of guided bearings, one should understand the movement of curved region of a prestressed bridge. Movement of prestress and creep are tangential to the curvature of the bridge (or along longitudinal axis) while the movement due to temperature and shrinkage effects are in a direction towards the fixed pier. If the direction of guided bearings is aligned towards the fixed bearing in the abutment, the difference in direction of pretress and creep movement and the guided direction towards fixed bearing would generate a locked-in force in the bridge system. The magnitude of the lock-in force is dependent on the stiffness of deck and supports. If the force is small, it can be designed as additional force acting on the support and deck. However, if the force is large, temporary freedom of movement at the guided bearings has to be provided during construction.
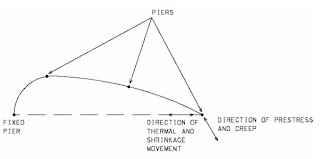 |
The diagram showing how the guided bearings in piers of the curved region is oriented with respect to the fixed bearing in abutment.
|
11. In the construction of a two-span bridge (span length = L) by using span-by-span
construction, why is a length of about 1.25L bridge segment is constructed in the first
phase of construction?
Basically, there are mainly three reasons for this arrangement:
(i) The permanent structure is a statically indeterminate structure. During construction by using span-by-span construction, if the first phase of construction consists of the first span length L only, then the sagging moment in the mid span of the partially completed bridge is larger than that of completed two-span permanent structure. To avoid such occurrence, 0.25L of bridge segment is extended further from the second pier which provides a counteracting moment, thereby reducing the mid-span moment of the partially completed bridge.
(ii) The position of 1.25 L countering from the first pier is the approximate location of point of contraflexure (assume that the two-span bridge is uniformly loaded) in which the bridge moment is about zero in the event of future loaded bridge. Therefore, the design of construction joint in this particular location has the least adverse effect on the structural performance of the bridge.
(iii) In case of a prestressed bridge, prestressing work has to be carried out after the construction of first segment of the bridge. If the prestressing work is conducted at the first pier which is heavily reinforced with reinforcement, it is undesirable when compared with the prestressing location at 1.25L from the first pier where there is relatively more space to accommodate prestressing works.
Note: Span-by-span construction means that a bridge is constructed from one bridge span to another untill its completion
12. What are the advantages of piers constructed monolithically with the bridge deck over usage of bearings?
Basically, piers constructed monolithically with the bridge deck are advantageous in the following ways:
(i) Movement of the bridge deck is achieved by the bending deformation of long and slender piers. In this way, it saves the construction cost of bearings by using monolithic construction between bridge deck and piers. Moreover, it is not necessary to spend extra effort to design for drainage details and access for bearing replacement. On the other hand, in maintenance aspect substantial cost and time
savings could be obtained by using monolithic construction instead of using bearings as bridge articulation.
(ii) Monolithic construction possesses the shortest effective Euler buckling length for piers because they are fixed supports at the interface between bridge deck and piers.
Note: Monolithic construction means that piers are connected to bridge decks without any joints and bearings.
13. Are diaphragms necessary in the design of concrete box girder bridges?
Diaphragms are adopted in concrete box girder bridges to transfer loads from bridge decks to bearings. Since the depth of diaphragms normally exceeds the width by two times, they are usually designed as deep beams. However, diaphragms may not be necessary in case bridge bearings are placed directly under the webs because loads in bridge decks can be directly transferred to the bearings based on Jorg Schlaich & Hartmut Scheef (1982). This arrangement suffers from the drawback that changing of bearings during future maintenance operation is more difficult. In fact, diaphragms also contribute to the provision of torsional restraint to the bridge deck.
14. What is the advantage of sliding bearings over roller bearings?
In roller bearing for a given movement the roller bearing exhibit a change in pressure centre from its original position by one-half of its movement based on David J. Lee. However, with sliding bearing a sliding plate is attached to the upper superstructure and the moving part of bearing element is built in the substructure. It follows that there is no change in pressure center after the movement.
15. What are the three major types of reinforcement used in prestressing?
(i) Spalling reinforcement
Spalling stresses are established behind the loaded area of anchor blocks and this causes breaking away of surface concrete. These stresses are induced by strain incompatibility with Poisson’s effects or by the shape of stress trajectories.
(ii) Equilibrium reinforcement Equilibrium reinforcement is required where there are several anchorages in which prestressing loads are applied sequentially.
(iii) Bursting Reinforcement Tensile stresses are induced during prestressing operation and the maximum bursting stress occurs where the stress trajectories are concave towards the line of action of the load. Reinforcement is needed to resist these lateral tensile forces.
16. Why is the span length ratio of end span/approach span to its neighboring inner
spans usually about 0.75?
From aesthetic point of view, an odd number of spans with a decrease in length in the direction of abutment is desirable. Moreover, spans of equal length are found to be boring. However, the arrangement of irregular span lengths is not recommended because it gives a feeling of uneasiness. From structural point of view, for a multi-span bridge with equal span length, the sagging moment at the mid-span of the end span/approach span is largest. In order to reduce this moment, the span length of end span/approach span is designed to be 0.75 of inner spans.However, this ratio should not be less than 0.40 because of the effect of uplifting at the end span/approach span support.
Note: End span refers to the last span in a continuous bridge while approach span refers top the first span of a bridge.
17. In the design of a simply supported skew bridge, which direction of reinforcement
should be provided?
In the conventional design of steel reinforcement for a simply supported skew bridge, a set of reinforcement is usually placed parallel to free edge while the other set is designed parallel to the fixed edge. However, this kind of arrangement is not the most efficient way of placing the reinforcement. The reason is that in some parts of the bridge, the moment of resistance is provided by an obtuse angle formed by the reinforcement bars which is ineffective in resisting flexure. In fact, the most efficient way of the arrangement of reinforcement under most loading conditions is to place one set of bars perpendicular to the fixed edge while placing the other set parallel to the fixed end as recommended by L. A. Clark (1970). In this way, considerable savings would be obtained from the orthogonal
arrangement of reinforcement.
 |
The arrangement of reinforcement in skewed bridge |
18. What are the functions of grout inside tendon ducts?
Grout in prestressing works serves the following purposes:
(i) Protect the tendon against corrosion.
(ii) Improve the ultimate capacity of tendon.
(iii) Provide a bond between the structural member and the tendon.
(iv) In case of failure, the anchorage is not subject to all strain energy.
19. What is the consideration in selecting the orientation of wing walls in the design of bridge abutments?
There are three common arrangements of wing walls in bridge abutments based on Dr.
Edmund C Hambly (1979):
(i) Wing walls parallel to abutments This is the simplest and shortest time to build but is not the most economical design. This design has the advantage that it has least disturbance to existing slope embankment.
(ii) Wing walls at an angle to abutments This is the most economical design among the three options in terms of material cost.
(iii) Wing walls perpendicular to abutments Though it is not the most economical design, the wing walls provide a continuous
alignment with bridge decks which provide supports to parapets. However, they cause disturbances to adjacent structures and utility services during construction. Moreover, if the bridge is curved, the wing walls may hinder the road curvature. One the other hand, when the wing walls are structurally connected to the abutment, then structural advantage can be taken by the stability of box structure
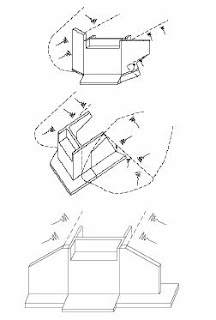 |
Different orientation of wing walls. |
20. In joints of precast concrete bridge segments, what are the functions of applying epoxy adhesive?
Epoxy adhesive is applied in these joints for the following purposes according to International Road Federation (1977):
(i) It seals up the joints completely between precast concrete segments to protect the prestressing tendons;
(ii) By filling voids and irregularities along the segment joints, it helps to reduce stress concentrations otherwise it will be developed; and
(iii) It helps in transferring of shear between the joints in case a large single shear key is used.
21. Under what situation should engineers use pot bearings instead of elastomeric
bearings?
In the event of high vertical loads combined with large angle of rotations, rubber bearings are undesirable when compared with pot bearings. For instance, elastomeric bearings require large bearing surfaces so that compression can be maintained between the contact surfaces between the bearings and piers. Moreover, it also leads to uneven distribution of stress on the piers and some of these highly induced stresses may damage the piers. Consequently, pot bearings are better alternatives than elastomeric bearings in such an scenario as suggested by David J. Lee.
22. What are the shortcomings of grillage analysis which is commonly used in structural analysis of bridges?
Grillage analysis suffers from the following shortcomings based on E. C. Hambly:
(i) For coarse mesh, torques may not be identical in orthogonal directions. Similarly, twists may differ in orthogonal directions.
(ii) Moment in any beams is mainly proportional to its curvature only. However, moment in an element depends on the curvatures in the beam’s direction and its orthogonal direction.
23. Polytetrafluoroethylene (PTFE) is commonly used in sliding bearings. Why?
The choice of sliding surface of bearings is of vital importance because the sliding surfaces generate frictional forces which are exerted on the bearings and substructure of the bridge. For instance, PTFE and lubricated bronze are commonly choices of sliding surfaces for bearings. PTFE is a flurocarbon polymer which possesses good chemical resistance and can function in a wide range of temperature. The most important characteristic of this material is its low coefficient of friction. PTFE has the lowest coefficients of static and dynamic friction of any solid with absence of stick-slip movement (David J. Lee). The coefficient of friction is found to decrease with an increase in compressive stress. However, PTFE do have some demerits like high thermal expansion and low compressive strength. In designing the complementary contact plate with PTFE sliding surface, stainless steel plates are normally selected where the plates should be larger than PTFE surface to allow movement without exposing the PTFE. Moreover, it is recommended that the stainless steel surface be positioned on top of the PTFE surface to avoid contamination of dirt and rubbish. Lubricants are sometimes introduced to reduce the friction between the PTFE surface and the upper stainless steel plate. Hence, the PTFE may be designed with dimples to avoid the lubricant from squeezing out under repeated translation movements.
24. Should raking piles of a bridge abutment be placed under an embankment?
For a bridge abutment to be supported on raking piles with different orientations, the movement between the ground and the pile group is difficult to predict. For instance, if some of the raking piles of the bridge abutment are extended beneath an embankment, then the settlement of embankment behind the abutment may cause the raking piles to experience severe bending moment and damage the piles as recommended by Dr. Edmund C Hambly (1979).
25. How do engineer determine the number of cells for concrete box girder bridges?
If the depth of a box girder bridge exceeds 1/6 or 1/5 of the bridge width, then it is recommended to be designed as a single cell box girder bridge. However, if the bridge depth is smaller than 1/6 of the bridge width, then a twin-cell or multiple cell is a better choice as suggested by Jorg Schlaich & Hartmut Scheef (1982). However, one should note that even for wider bridges with small depths, the number of cells should be minimized because there is not much improvement in transverse load distribution when the number of cells of box girder is increased to three or more.
26. What is sucker deck principle for variable depth bridge decks?
For a variable depth bridge deck, the depth of continuous multi-span bridge deck is increased in pier supports and this absorbs sagging moments in the mid-span with the consequent increase in hogging moments in pier supports. As a result, the mid-span depth can be significantly reduced due to the reduction in sagging moment. In essence, this sucker deck principle is applied in locations where headroom requirement is of great concern. Moreover, in terms of structural performance, sucker decks are effective in reducing dead loads than voided slab of equivalent uniform depth for span length between 20-40m. In terms of aesthetics point of view, the public tends to appreciate the structural
form of arches and curved soffit rather than boring uniform deck alignment. Reference is made to Brian Pritchard (1992).
No comments:
Post a Comment
If you are getting more information from civilengineerfriend page please give your comments. Share the page information in your whatsapp group. Subscribe our page to get more information.